SCHEDULE AND AVAILABILITY: This is an update as of 11/6/2024.
IMPORTANT NOTICES:
Please be aware that the waitlist is now CLOSED to new business outside of our local area but will re-open in January 2025. We are considering exceptions, so contact us with questions.
Be aware of our 2024 holiday hours. While we will be here hard at work, we aren’t accepting any new projects or shipments in the door until January 2025. Product shipments may be delayed somewhat, but we will do our best to keep them going out the door for you.
If you are already on the waitlist, please keep in mind that it’s up to you to follow up with us after being added to it. We will do the best we can to accommodate you.
Please note that our shipping policy has changed (well, about 2 years ago). So we consider this a gentle reminder. Please review it here before dropping off any clock that will not fit in a 26″x26″x20″ box:
Updated Shipping Policy as of December 2020
Lastly, we want to once again sincerely thank all of you who have previously sent us new projects!
Policies of Common Courtesy:
Policy on Rudeness, Bullying or Abusive Communication from Customers. We don’t want to make this sound onerous. But sadly, in today’s (unnecessarily) charged-up world where rudeness seems to be “acceptable,” and folks hide behind emails, Instagram, FB or X posts, etc., we find it necessary to restate the seemingly obvious. This work is a labor of love, and we do not wish it to become otherwise. We have never found bullying acceptable and never will. We strive to provide your cherished clock with the utmost loving care possible. If, in return for that effort, you choose to call or email and become rude or verbally abusive despite our clearly stated backlog policy, we will return your project and wish you the best of luck. We may alternatively apply a rush charge to your project in lieu of returning it (if it has already been started) in cases of rudeness. We understand you may be anxious to see your project completed; no one likes to wait –and neither do we. If you are anxious, we want to be attentive to your needs and will be more than happy to help you. It’s simple, and it’s called common courtesy–we do not accept e-treatment that you wouldn’t apply in person.
Policy on Phone and Email Support. We understand that when movements are returned, there may be questions about connections and other issues that arise. We are very happy to help with these issues! A few emails and perhaps a call evaluating pictures and responding to observations is considered acceptable. However, we have seen situations where our generosity and support were exploited. Therefore, as of May 1, 2022, we are forced to charge a flat $120 service charge for extensive support, defined as more than two telephone calls AND 4 emails. Compensation for this level of effort is industry standard. And, nearly 100% of the issues we end up solving are related to mishandling of the clock or movement on the customer’s end.
Policy on Billing. The world of clock restoration is not what it once was. No longer can one take in a project, change some parts, and send it off. Multiple parts must be hand (sometimes custom) made nearly 100% of the time and when they cannot be made here, someone must be found to help. Unexpected problems crop up that are nearly impossible to foresee. While we can offer ballpark ranges, we cannot offer exact quotes before the work commences and often details are not known until the project is nearing completion. We always do our absolute best to stay within our ballpark ranges. If anything comes up above that, we will communicate that to you before proceeding. We strive to prevent surprises.
If there is any confusion on billing, we are happy to work with you to resolve it in a polite and civilized fashion. Rudeness as stated above in our Policy on Rudeness, Bullying and Abusive Communication cannot be tolerated, nor will baseless “negotiations” be engaged. Warranty may be forfeited in cases of rudeness or we may ask that you kindly take any future business elsewhere. We will always be respectful of you, treat your article with utmost care, and expect no less in return.
Policy on Powering SWCC Movements with cheap battery holders and alligator clips. If you choose to use a custom power supply of your design or selection that is not something we recommend, we are happy to review it for interoperability and proper connectivity, to avoid damage to the movement that would otherwise not be covered under warranty.
The problem is, customers call or email claiming a fully restored movement is inoperative when reliable connections and power sources are not established. It is impossible to warranty a movement powered by poor quality battery holders or connections involving alligator clips. Experience has proven that alligator clips are NOT a reliable way to connect a self winding clock movement for the long term. Thin, twisted, taped wires from poor quality (or corroded) battery holders compound the problem. We have all the correct material available to you for a very reasonable charge. Compare that to the cost of shipping a movement back and forth multiple times to find a problem that doesn’t exist.
Policy on Pricing. This gets asked multiple times per day, so we thought we would provide this:
As a guideline, restoration fees will typically follow this schedule: Pricing Schedule
Pieces that don’t fall into the above categories will need to be quoted upon receipt. Keep in mind that the above are sight-unseen guidelines. They are not firm quotations.
If for whatever reason you cannot abide by the above policies, we will be disappointed but understand that you may wish to go elsewhere, and will wish you the best of luck.
Note on Plating Services: We no longer offer piece-parts plating for those wishing to do their own clock restorations (such as cases, weight shells, pendulums, bezels, dial pans, etc). We continue to offer plating as part of in-house clock restorations, which is our core business. The driving factor is it distracts from reducing our clock restoration backlog; it is not our responsibility to reduce others’ backlogs. We also have no idea if those parts are ever installed in a clock vs. being sold for steampunk or something else.
Our Story. Ken’s Clock Clinic is the #1 choice when it comes to your clock restoration needs. Our services include restoration of vintage American and European wall clocks, mantel clocks, cuckoo clocks, electric clocks, self winding clocks, and many others. We rebuild movements, restore wood or metal cases, touch up dials, or perform a complete clock restoration. All movement restorations are backed by a two-year warranty.
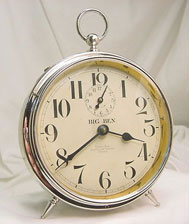
We service antique 8-day American clocks such as Ingraham, Gilbert, Lux, Sessions, New Haven, Seth Thomas, Herschede, Waterbury, and many others. We service Vienna Regulators, English bracket clocks, Crystal Regulators, Self Winding clocks, highly collectible alarm clocks, vintage and contemporary cuckoo clocks, and vintage electric clocks. Our experience and techniques allow us to properly–and with the utmost standard of craftsmanship–service and restore clocks which are difficult to work with. A great deal of our work involves reversing improper or amateur repairs done over the years by others, resulting in an as-new clock that will be serviceable for many, many years.
A Note on “Full Restoration.”
First, note that we do not “refurbish” movements since that term refers to renovation, not restoration. Either way, we find that some folks are frightened by the term “restoration.” We are sometimes asked to do “just a simple cleaning and oiling” on a 100 year old vintage movement. If we are presented with a relatively un-worn, newer (less than 10 year old) movement, things may be different. But a vintage, 100 year old movement is going to have many looming issues, always. Anything less than a full restoration is a piecemeal repair, and piecemeal work cannot be offered with any long-term warranty, if it works reliably at all. It is not the standard of craftsmanship we are known for.
A piecemeal approach results in call backs more times than not, which means the movement or entire clock will need to be shipped back and forth at least once. This alone will nullify any economic advantage to doing anything less than a full restoration. We don’t consider any clock that runs for only 6 months or year after a repair is done a successful project.
In addition:
1. Movements that require cleaning and oiling need to be fully disassembled (down to the individual wheels, pillars, screws, etc). While disassembled, this is when wear (as well as previous botched repair attempts) should be addressed. There is no half way in dealing with these issues.
2. Removing the movement from the case always reveals more surprises than cursory inspections from the back (or front).
3. Mainsprings need to be removed from the barrels and inspected (possibly replaced) before anyone can judge their condition. If we send you back a clock where this has not been done, it’s a time bomb. Most clocks require full disassembly to do this. Once it is fully disassembled, again it is folly to do any less than a full restoration. Experience has shown that if original mainsprings are re-used, the chance of breaking in the near future is very significant.
4. Pivots need to be polished to a glass-like smoothness, and holes rebushed so as to be clean and undetectable. Precision reamers are used to achieve exact pivot-to-hole fit and clearances. These are among the most important steps. Rebushing holes without polishing pivots leads to premature hole failure, and furthers additional pivot wear. Using traditional broaches alone to open holes can lead to geometrically distorted holes. Worse yet, leaving worn holes unaddressed is a sure path to unreliable performance.
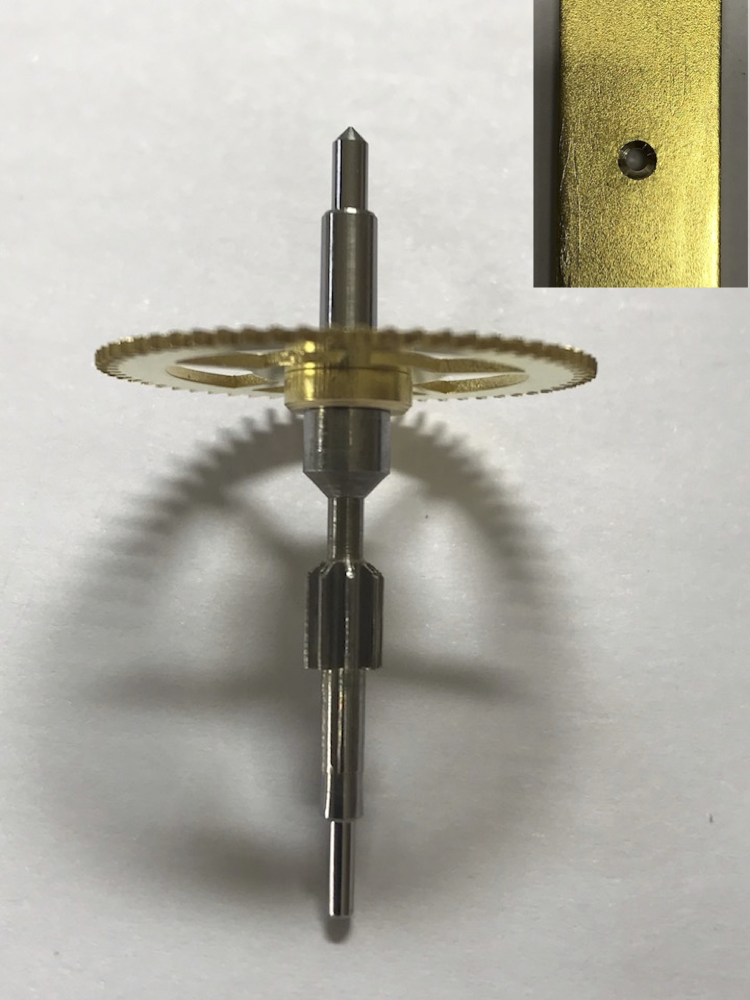
Once a clock is fully restored by us, it will generally run for perhaps 10-15 years or more with nominal maintenance (oiling and adjusting ever 3-4 years). After 10-15 years, more work may be needed, but this is variable. By contrast, simply oiling a 100 year-old worn out movement does not remove the wear or provide any longevity. If only oiled, the clock may function (short term) but cannot be warranted.
That’s the rationale behind why we generally recommend full restorations. Obviously, there are bound to be exceptions, but this is what we have found to be the case in a very high percentage of the vintage clocks and clock movements we see.
We don’t want to see your clock back here every 6 months! We are aware that there are folks out there who use this as a strategy for staying in business. We don’t.
While we would love to help (and will), if you are set on a piecemeal repair, there are probably other houses that will engage in this folly–but your prized item and you will suffer. We’ve learned our lesson over and over on taking a piecemeal approach, and it ultimately doesn’t make sense for either us or the customer. You won’t be happy with piecemeal repairs long term, and we’ll get tired of unpacking and packing your item!
“All It Needs is a Good Cleaning.”
There is quite a bit of mis-information out there that “all a movement needs is a good cleaning.” In our experience, that is 5-10% of the total work needed to properly restore a movement. There are proper ways to clean a movement and destructive ways, and the line is very fine between them.
The majority of the work that goes into getting a movement operational involves, but is not limited to, plate work, precision pivot polishing, escapement restoration, balance cup or jewel restoration (not for the faint of heart), fabricating replacement parts such as clicks, arbors, replacements for worn wheels, cannon pinions, etc., as well as mainspring maintenance which is tricky these days since the selection of replacement mainsprings out there is at an all-time low.
Please avoid the temptation to start the project on your own, thinking we can “rescue” it if things go wrong for you (and they more often than not do). A gentle, careful dust off for purposes of taking pics is a great idea. But if you wish for us to work with you down the road, it would be best to avoid going too much further than that, since too many bad things can subsequently happen. We have had folks attempt “repairs” on perfectly good coils, ruining them, requiring an expensive rewind. We’ve also seen lost parts requiring fabrication to replace, bent or broken pivots, and other expensive-to-repair damage. Don’t be tempted to do it!
Self Winding Clocks.
While these beautiful, cherished clocks are self-winding, they are not self-maintaining. Many owners seem surprised when a clock that has been working for 30 years suddenly stops. Inquiry reveals that the clock was never oiled, contacts cleaned, or even inspected for wear. It’s not unusual; self winding clocks manufactured in the early 1900’s were designed to be operated in fairly adverse industrial environments. Retired to the safe environment of the home, they tend to have longevity. Unfortunately by the time they make their way to our shop door, they are extremely worn and in need of a great deal of work due to lack of maintenance.
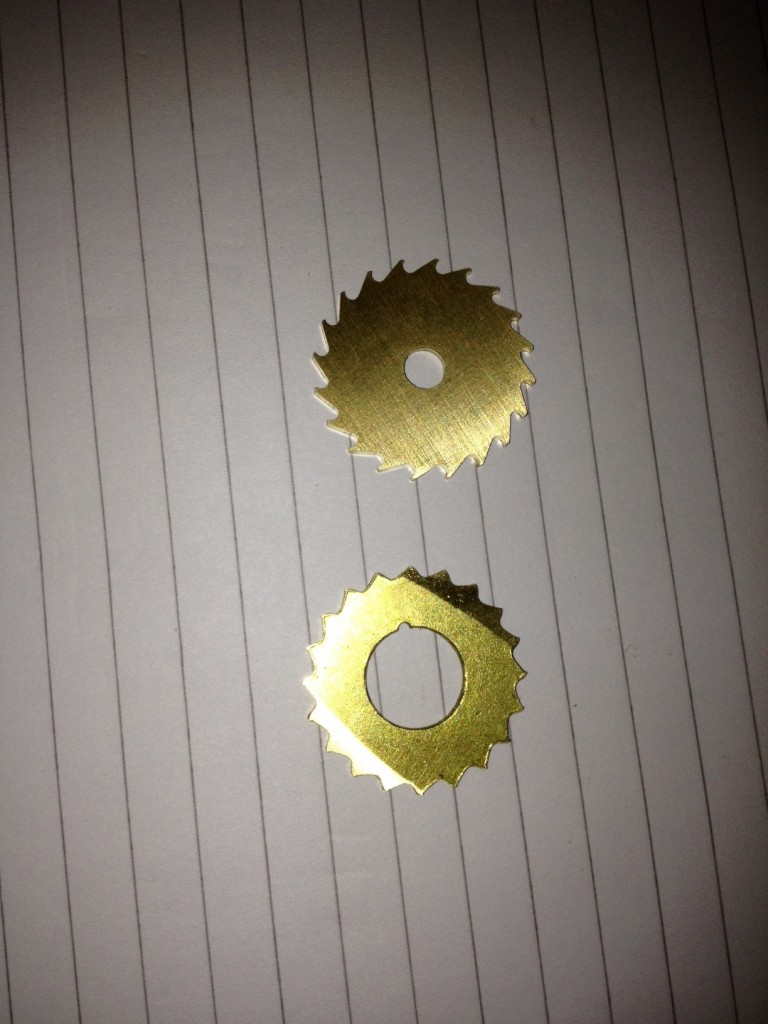
Mechanical wear must be addressed in a variety of ways. The challenge for the clock repair person is the level of custom machining and fabrication that is needed to carry out the repairs on self winding clocks. There is also the need to fabricate custom platinum contact replacements as well as assess and restore other electrical elements. We are fully equipped for this challenge, and have been from the beginning. Without this capability, one cannot restore self winding clock movements with routine success. In more conventional clocks, this wear is dramatically less since run time is often interrupted by weights or springs running down. And, of course, conventional clocks do not have electrical contacts and related elements.
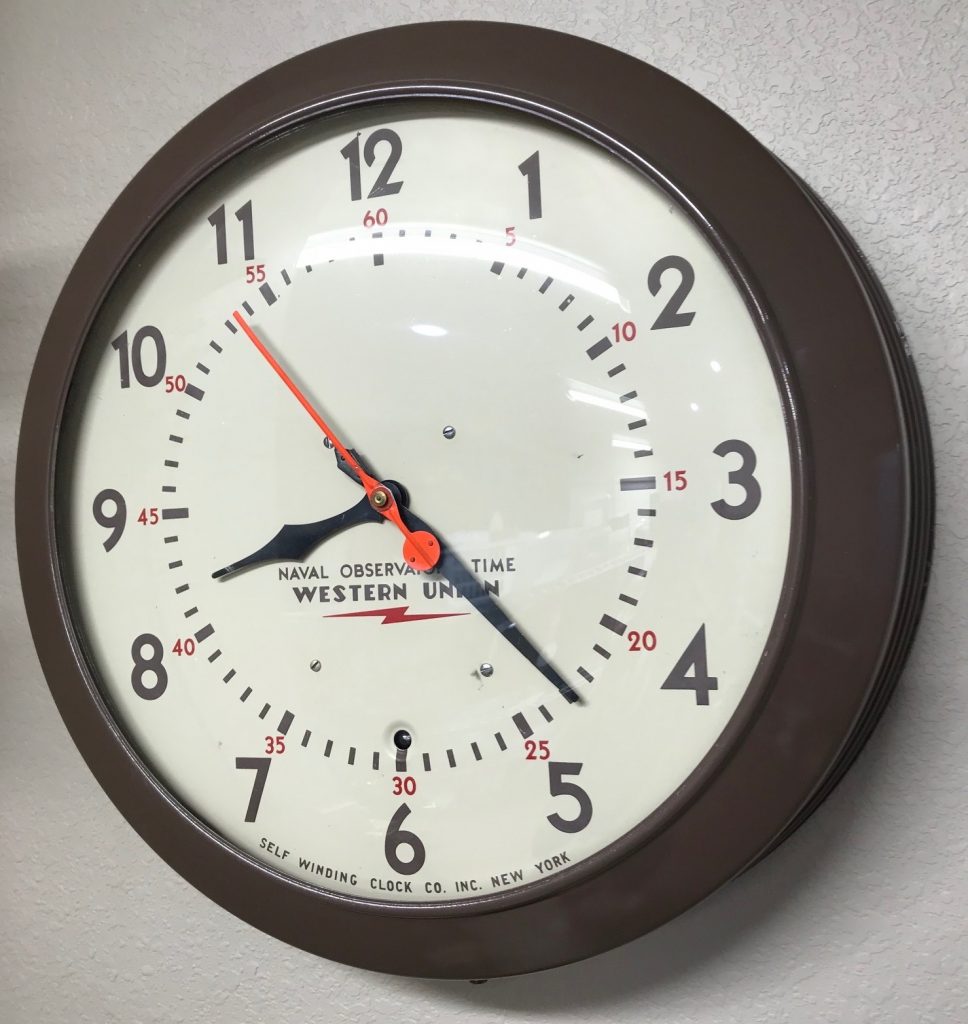
Our experience, custom replacement components, and equipment allows us to take a no-compromise approach with your restoration. We can fabricate any component of the clock, and often we need to fabricate replacement parts because the originals have worn so excessively. We stock many common wear parts (such as spring contacts, brushes, Style A/B/C hourly contacts and backstop springs) manufactured from drawings meticulously created from original parts by us. And of course, we stock the “raw materials” to fabricate parts that are not available. This includes the proper alloys of brass, bronze, beryllium copper, steel, precious metals, resin plastics, copper and resistive wire, other electrical components, etc.
Self winding clocks are generally powered by relatively weak springs–or no springs at all, so they tend to wear slowly. However, the flip side of this is that they tend to run for long periods of time without rest. By contrast, a conventional spring or weight-powered clock will run down and perhaps be left without winding for extended periods of time. Moreover, many self winding clocks were poorly maintained because most clock repair folks were not familiar with them and would either avoid them or could not professionally address unfamiliar wear specific to these clocks.
With Self Winding Clock Co. units, there was a tendency to use hole closing punches on both sides of the plates, which left the bearing surfaces thin and more subject to wear. We address these issues in every restoration, returning a clock that is virtually like new. See our 25-Step Restoration Process for Style F document, which outlines the detailed process used for Self Winding Clock Co. Style F (the most common) movements. Or, learn more about the details of our SWCC Restoration Process for Style A/B/C movements. If we restore your movement, you will NEVER see ill-fitting or out of center bushings protruding from the plates, unpolished pivots, or any other form of butchery that is common with many shops today.
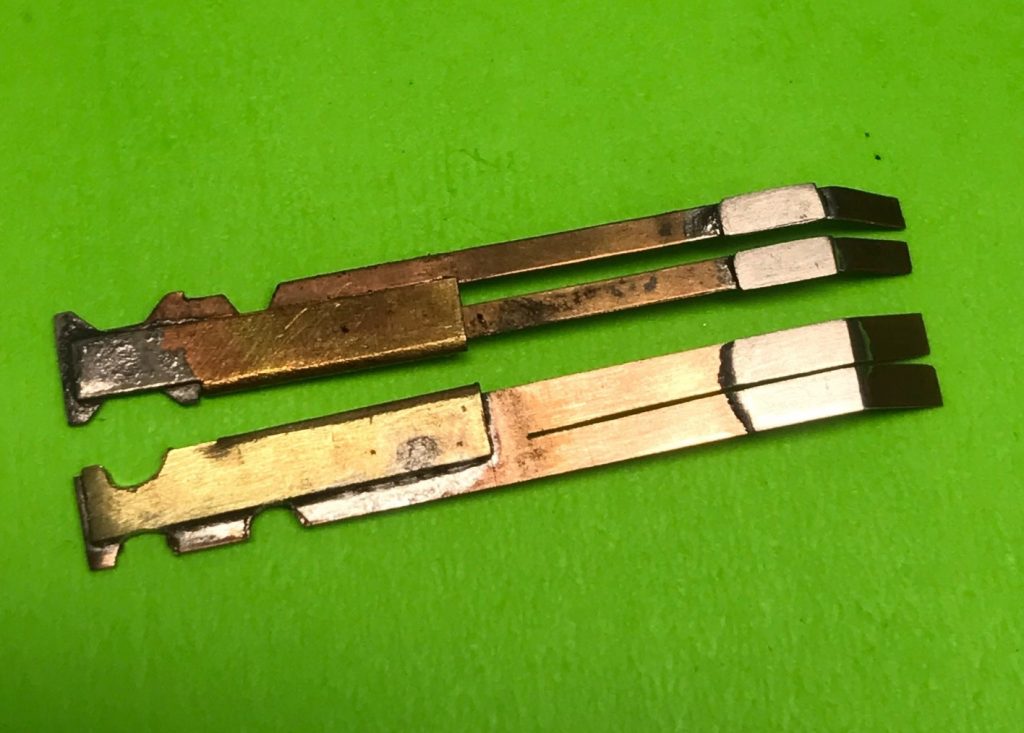
And yes, we now do indeed have the capability to fully restore the small German die-cast motors found in the more recent Broadcast Studio clocks. We can safely and harmlessly disassemble the motor, fabricate replacement commutators, bifurcated brush assemblies, and of course can re-tip the brushes with .004″ platinum (3x the original thickness!). The result is an all-original motor restoration with longer life than the originals.
We are able to provide GENUINE silk-covered rewinds for Style A/B/C motor coils and resistors, which replicates the originals exactly! This reflects our continued commitment to improve the quality of our period-accurate restorations on these unusual and cherished clocks.
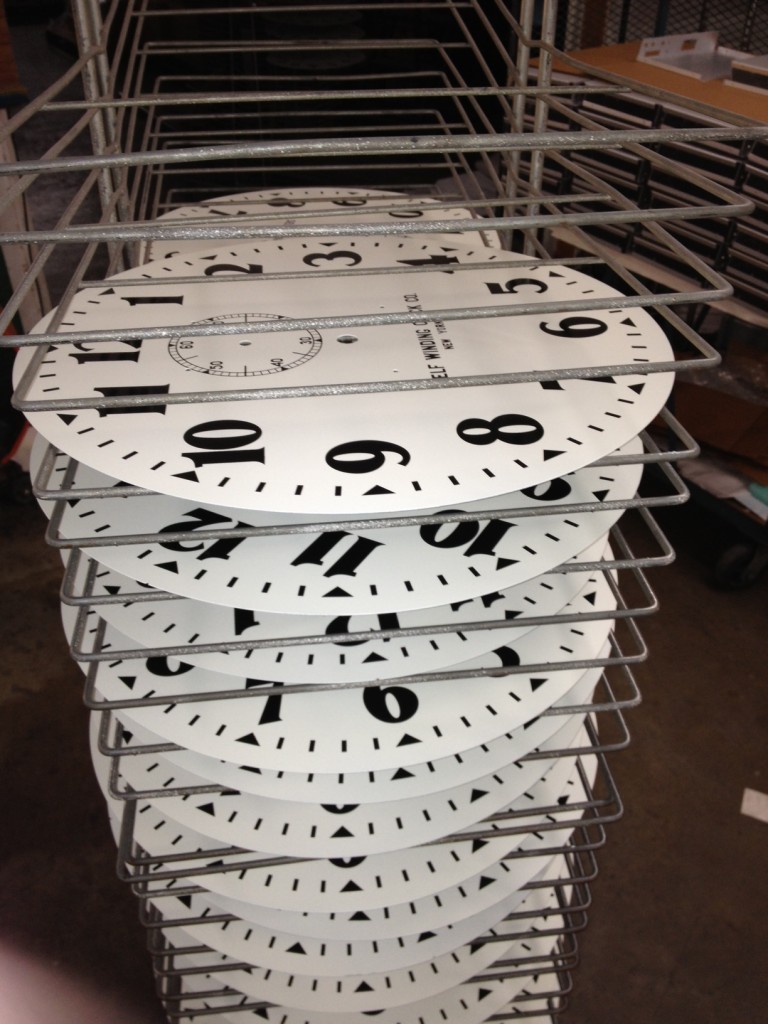
Telechron, Revere, New Haven, Hammond, Sessions Electric Clocks.
We fully restore original electric clock movements such as Telechron, Revere, GE, Hammond, Sessions, Seth Thomas and others. We can rewind coils, fabricate replacement fiber wheels, and completely rebuild and restore Telechron rotors as part of the clock restoration. We NEVER replace movements with quartz or others, and we never take short cuts with rotor restorations. We may be the only service left on the planet that can fully restore a Sessions electric chime clock! That’s because almost 100% of them require new coils–which we can wind.
We have been asked if we service vintage New Haven electric clocks. The answer is a resounding yes! These are very rewarding clocks to restore (and are among our favorites), as many case styles were unique and fashionable in their time. Also, New Haven engineered many very clever features into their movements. These are often overlooked because the small size and stacked plates sometimes leave the perception of complexity, which scares many away. We can restore both New Haven electrics as well as the key-wound (No. 380) triple plate chime or strike movements. We can fabricate replacement parts for these movements, and often this is necessary for a proper and thorough job. No issue with these is outside of our capability.
It is nearly impossible to change the cord on a standard Hammond movement. This is because it is very tight in the area where the cord exits, and the coils were originally wired directly to the cord with no room for any kind of repair. We can carefully open the coil, expose the original leads, layer on special high voltage transformer tape, adjoin the new cord exactly as the original, then re-insulate and finally re-cover the coil. Original outside coil dimensions are maintained (and NO, we NEVER use black electrician’s tape, which should NEVER be used in clock restoration). It would be very difficult to tell that we were ever in there. The process is literally surgical and done under a microscope in many cases. If something goes wrong (the fine #40 wire found to be broken or the coil discovered to be open), we can rewind the coil. Few if any shops have the tools, materials, skill and training to attempt this, and certainly rewinding coils is outside the competency of any other clock repair shop.
Hammond Bichronous.
Yes! We restore Hammond Bichronous electric movements, and will deliver them back to you in as-new working condition. We understand these movements in all aspects and can address every failure issue. Yes, they are challenging and time-consuming restorations, but quite manageable.
Hammond Bichronous are unique movements. Their unusual feature is that if power is lost, the movement continues to run on mainspring power for up to 30 minutes! This is accomplished with a separate rotor and wheel train which winds the mainspring, stacked on top of the standard synchronous gear train which drives the hands. This tandem gear train creates unusual restoration challenges, with dual fiber wheels and fiber bearing plates, all of which are worn or broken as found.
Of course, these great clocks were often housed in unusually beautiful cases, including some which were offered in the “Postal Telegraph” format–large wall clocks that are a joy to own and sought after by collectors. Many were originally sold to postal depots and other industrial customers. There don’t seem to be many left in circulation, so they are prized.
This is not the most economical restoration, so please contact us for typical pricing and lead time if you are interested in having your beautiful Hammond Bichronous electric clock restored.
If you are not familiar with the Hammond Bichronous, it’s a movement that has a unique function. If the power fails, the movement will continue to keep accurate time for up to 30 minutes, even without electrical power! It does so by combining a mainspring-driven movement with a standard synchronous electric movement, the two literally stacked in tandem on top of one another. We can address the fiber wheels, worn fiber bearing plates, and of course the challenging worn tandem arbors and internal bearings
Electric Clock Rotor and Motor Restorations.
Yes, we do restore rotors and motors for customer clocks here in our own shop. We do not send them out, and we don’t buy rotors restored by others. And, just as important, we NEVER replace a rotor with one of the commonly available, short-lived and noisy Chinese rotor replacements. We have developed our own techniques which we have found to work most reliably. In fact, many of the methods claimed by others do NOT work. For example, there is a common claim that you can force oil into a rotor through the shaft to oil it, with long life expectancy. That is only partially true; but having disassembled many H rotors, we have observed that this is simply not near enough.
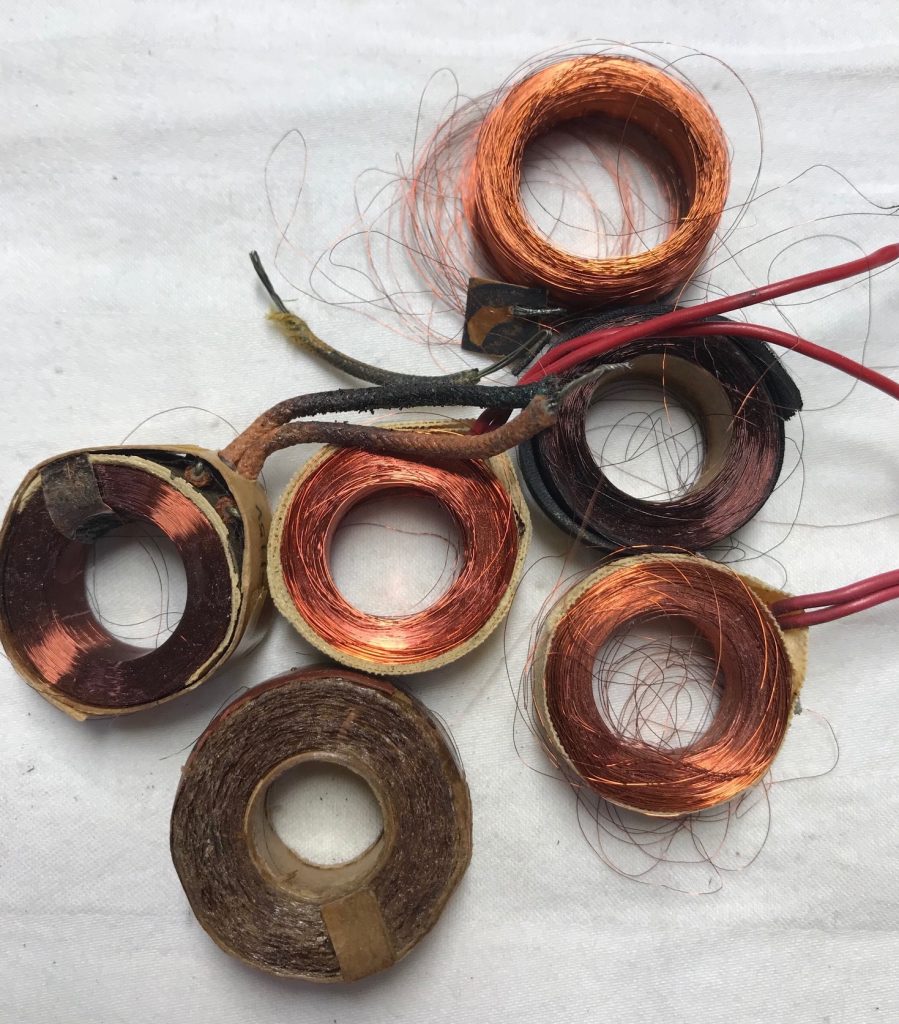
Internally, the oil inside these rotors dries into a varnish-thick sludge, and adding oil to varnished sludge or filthy oil does not help. Wear–or unreliable operation–will ensue. Further, if there is already wear, the rotor must be serviced before oiling makes any sense. This cannot be assessed without inspection of the movement inside the rotor case. In fact, about half of the H rotors we see require a new output shaft bushing, and sometimes a new output shaft as well. This cannot be cured by forcing oil into the rotor capsule!
With the dried oil and caked-on grease present on the output shafts, how can driving oil through this shaft (from the outside in) do any more than pack varnish-hard oil back into the case containing the watch-like rotor movement? And how can this do any less than foul the rotor and stop it eventually?
Older Telechron B rotors simply do not respond predictably to blind pressure (or any other kind of) oiling at all from the outside. There is always wear, and it must be addressed. Again, output bushings, shafts and internal plate holes are often worn, requiring disassembly and repair.
Hammond rotors always require opening up, output shaft bushings (and sometimes new output shafts), and sometimes new internal bushings, arbors, wheels or other parts fabricated. They cannot simply be oiled and put back into service.
With the much newer M5 General Time rotor capsules (often used in later model Seth Thomas chime clocks), wear will be present, but sometimes it can be lived with. Other times, wear is extensive and no amount of oiling will help. If an M5 rotor is still operational, it may benefit from oiling. The amount of oil forced into the rotor must be measured very carefully. Over-oiling these tiny rotors will flood the rotor and stall it, or cause drag that affects timekeeping. Yes, we can also open and service M5 rotors, rebush the plates, restore worn arbors, reassemble, oil, and seal them back up again.
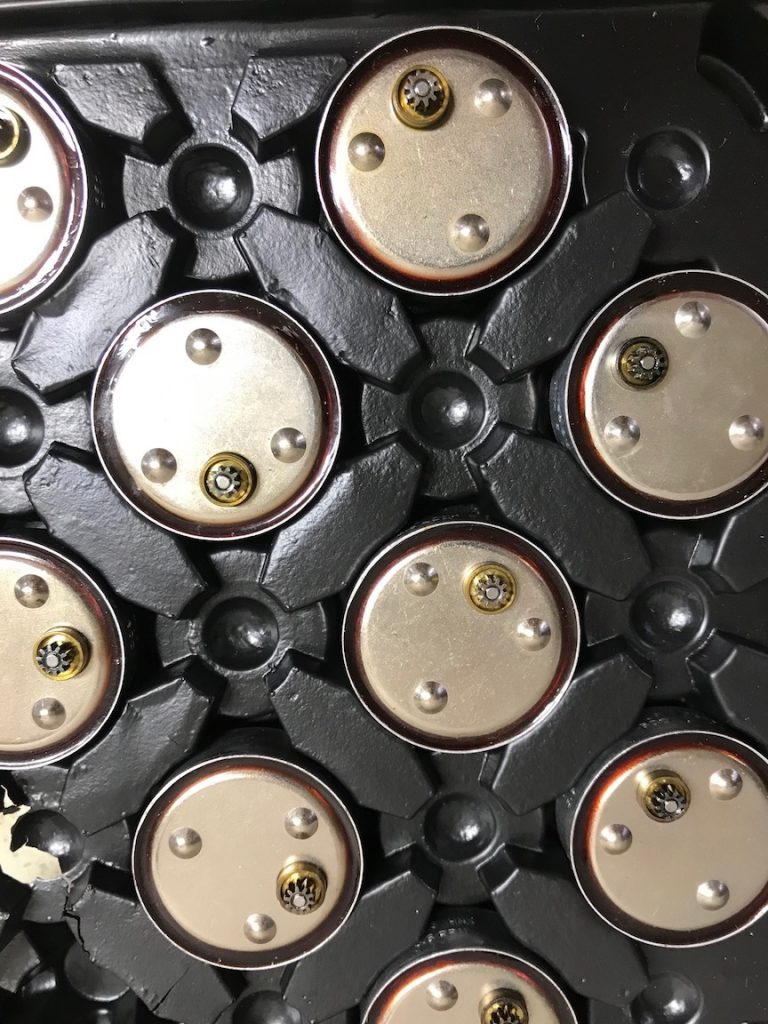
Although we do restore Telechron rotors for our own clock restorations, we do NOT offer a rotor-only restoration service. If you are looking for an excellent Telechron rotor-only replacement or restoration service, we are pleased to recommend www.telechronclock.com for courteous, conscientious and economical service. Dave will disassemble, clean, rebush and replace worn parts (B rotors), lubricate then reassemble. He stands behind his work with a very good warranty. We will consider restoring General Time and Hammond rotors, but prefer to do so only with the rest of the movement present, so we can assure the condition of both. Simply installing a functional rotor into a dirty, sludged up movement is a sure way to wear out the rotor in short order.
Sessions, United, and General Time open frame motors require a unique approach. The sintered bronze bearings were originally vacuum oiled during manufacture. Seventy to 80 years later, this oil is long gone and the bearings worn. Adding oil from the outside is folly if there is wear or dried lubrication within. We fabricate and install new replacement bearings as needed, clean and lubricate internally, and the prognosis has proven excellent. We can also open these motors, fabricate replacement bobbins and coils, then reassemble with excellent results.
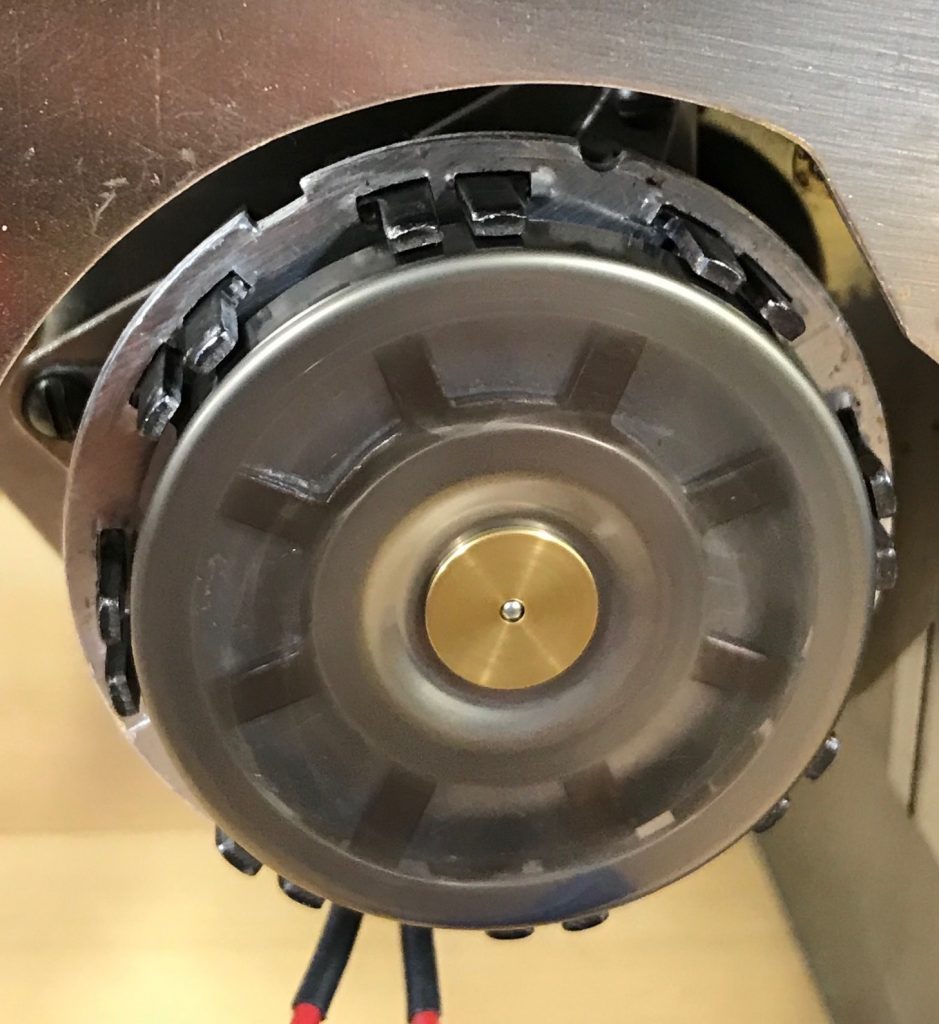
Synchron geared motors are used in many back lighted and neon clocks, as well as most “mystery” clocks. Sometimes replacements can be found. Most commonly, the 1 RPM RH motors (A43RA series) are still available. But most other shaft speeds are no longer available or are extremely difficult to find. We restore these motors by disassembling, fabricating replacement gears, bronze bearings and other parts to replace worn phenolic gears, worn “babbitt” or sintered bronze bearings, output bearings and shafts. Coils cannot be accessed with these motors, so availability of replacements is a blessing.
Electric Clock Coil Winding.
While some stock of standard Telechron coils exists, we can provide coil winding services for unusual electric clocks such as Windsor, New Haven, Telechron NuTone, Sessions chime clocks, General Time, and others. The movement is needed for this rewinding service since we must design and produce a custom winding bobbin for each movement.
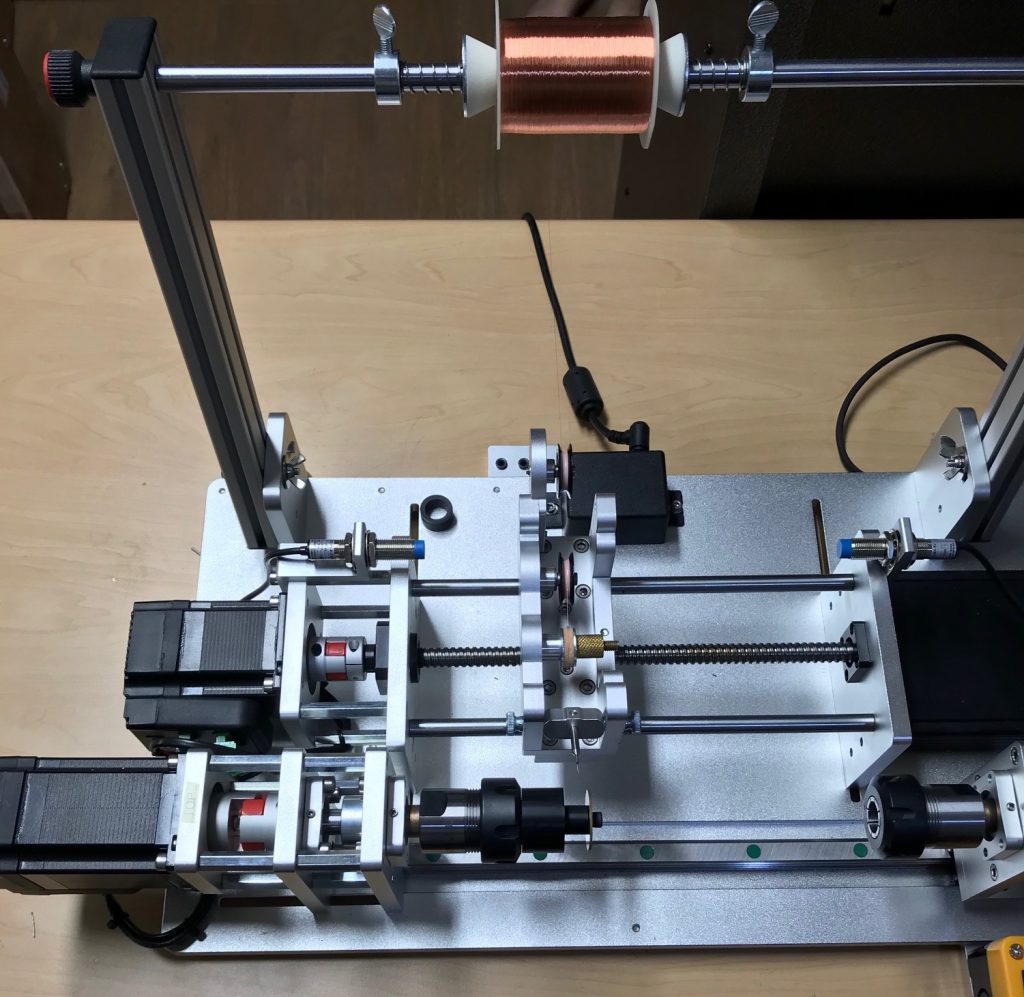
Cuckoo Clocks.
Yes, we service cuckoo clocks, contemporary and vintage. We have experience and expertise with restoring vintage cuckoo clocks, which are notably different than contemporary cuckoo clocks, and require a different approach. For example, ratchet wheels and other movement parts are often severely worn and require fabrication of replacements. We can replicate the originals exactly and bring any vintage cuckoo clock back to life again. We can repair worn music movements, returning the original tune to service. We understand that you love your cuckoo clock’s sound and want to return it to you with the same tune that you are accustomed to.
Many repair folks prefer to replace cuckoo clock movements instead of repairing the originals. While some movements are available and are quite close replicas to the originals, many are not. Further, original versions of these movements (Regula 25, 34 and Hubert Herr most notably) used brass wheels where replacements now use plastic. Notwithstanding, some rather unique versions are no longer available. For these reasons, we much prefer to restore the original movement whenever possible. There is rarely a reason to replace an original, high quality movement in any but the most extreme situations. The same applies to cuckoo clock music movements.
If your cuckoo clock has met with an unfortunate accident resulting in broken case parts and other damage, don’t worry. We can do case repairs and return your clock to its wall looking like new. We’ve restored damage to both vintage cuckoo clock cases as well as contemporary cuckoos.
Note on Travel Alarms (and similar watch-like) miniature clocks. Many travel and miniature clocks are actually watch movements in disguise. Movement parts are difficult (sometimes impossible) to make or find. Consequently, with apologies, success with travel alarms may be variable. Our equipment and experience with watch movements, while well above that of a typical clock repair service, still sets limits on what we can offer affordably. Leather cases cannot be restored in our shop. We see such minuscule demand for travel alarms that it is uneconomical to create any network for these services. That said, we have had some great success with these, but pricing can become a concern due to lack of availability of parts. These seem to fall into a dead zone between clocks and watches where hunting down parts can take almost as much time as the restoration itself, unfortunately. These must be quoted up front with the piece in hand.
Our Facility
We are equipped with precision machining tools, electronics assembly equipment, and a sophisticated plating area designed for small components. We perform restorations, case refinishing, and final system assembly in-house to ensure quality. We design our own replacement parts, No. 6 kits, winders, and closely monitor supplier quality. All products are proudly Made in USA.
Pricing
Pricing is commensurate with the amount of disassembly, restoration, and re-assembly required. However, we have a reputation for the highest quality work available yet reasonable rates. We back our craftsmanship with a standard 2 year warranty. Our extended warranty covers materials and workmanship for 5 years and includes one maintenance oiling during that period. Consider our Pricing Blog before you judge what is expensive or not.
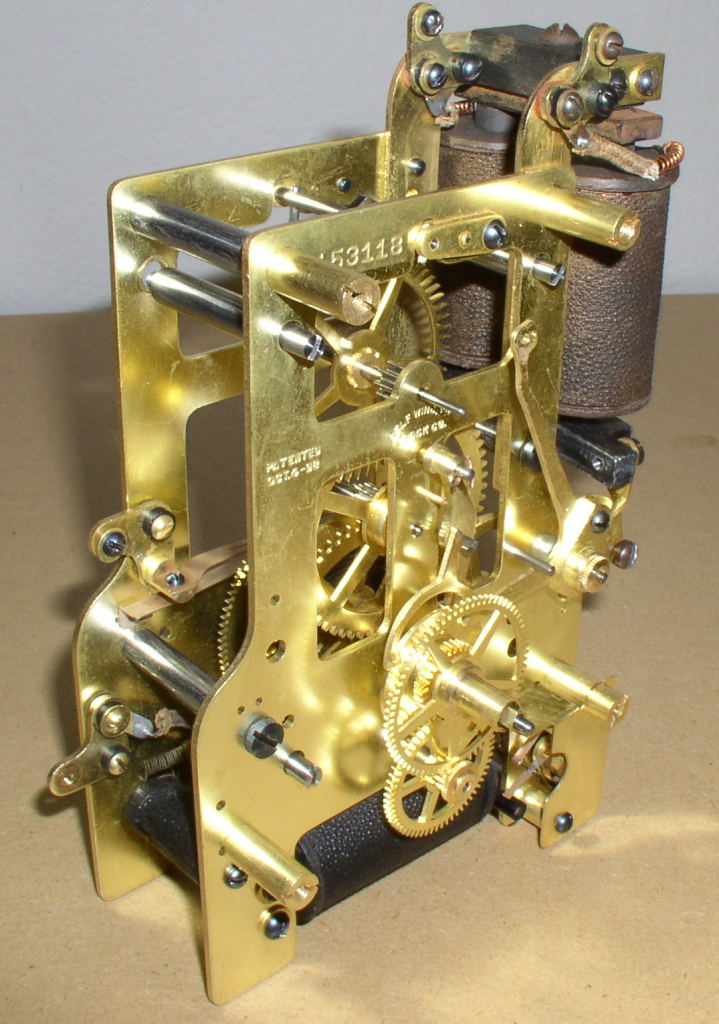
If you are considering restoration of low cost alarm clocks, please first consider our alarm clock forward. To arrange a quote after reading the Forward, please contact us. Minimum restoration charge for collectible alarm clocks (case and movement) is $250.
Policies on return shipping: Customer assumes responsibility for shipping and handling costs, regardless of reason. Restated, for clarity: Customer pays for return shipping and handling in all cases, including warranty returns. This is standard industry practice, and because we have no control over whether a return is a legitimate claim or not until the unit is inspected. Proper shipping and insurance can amount to a great deal of cost, so be sure you have a legitimate problem (and contact us for assistance) before returning your unit. From historic experience, very few warranty returns are a result of anything we did.
As of January 2019, return shipping on restored articles will include requirement for Adult Signature. No exceptions. With the apparent upswing in porch piracy, we must take action before someone’s valuable piece is lost. We apologize in advance for any inconvenience this might cause.
Reminder: Policy on Rudeness, Bullying or Abusive Communication from Customers. We strive to provide your cherished clock with the utmost loving care possible. If, in return for that effort, you choose to call or email and become pushy, rude or verbally abusive despite our clearly stated backlog (yes we have had this happen), we do not want your business. We will return your project and wish you the best of luck. We may alternatively apply a rush charge to your project in lieu of returning it, in cases of rudeness, at our discretion. We understand you may be anxious to see your project completed; no one likes to wait including us. If you are anxious, please ask us, in a kind and socially acceptable tone, to elaborate on its status, avoiding unnecessary sarcasm or subtle derogatory comments. We are attentive to your needs and will be more than happy to help you.